"Lautsprecherchassis reparieren? Geht denn das?"
"Ja, das geht! Aber nur, wenn's Ersatzteile gibt . . ."
. . . Billigtröten vom Elektronikversand kann man getrost wegwerfen, denn dafür gibt es mit Sicherheit keine Ersatzmembranen . . .
Aber für hochwertige PA-Chassis gibt es sie, und für einige wenige HiFi- und Car-HiFi-Chassis der oberen Preisklasse (z.B. FOSTEX, EMPHASER) kann man sie auch bekommen.
Wer keine zwei linken Hände hat, den Lötkolben auf Anhieb am richtigen Ende anfasst und auch sonst sehr sorgfältig arbeitet, kann's ja mal probieren. Einmal ist es immer das erste Mal . . .
Was man dazu unbedingt braucht:
Teppichmesser
Stemmeisen
Lötkolben, Lötzinn
Tesapack oder Gaffatape
dünne Pappstreifen (übrige Visitenkarten)
Einwegspritzen 10-20ml
Industriekleber (3M EC-1022 o.ä.)
Zweikomponentenkleber, der elastisch bleibt (Elefant oder Bindulin)
eine ebene Unterlage (Spanplatte o.ä.)
Hilfreich ist außerdem ein Heißluftherd (!)
GEDULD, ZEIT und dann natürlich einen defekten Bass und das zugehörige Repair-Kit . . .
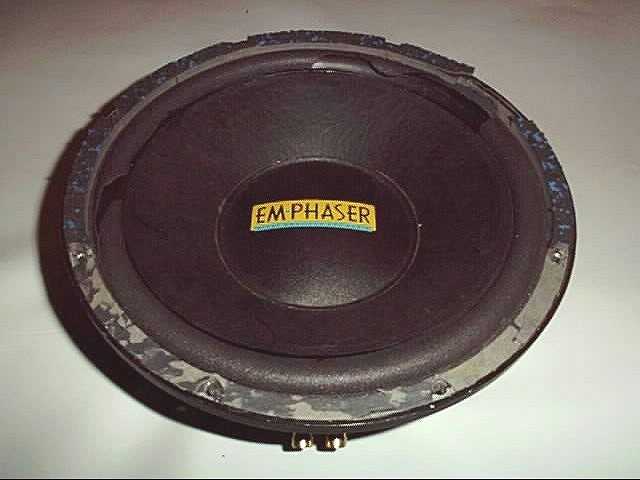
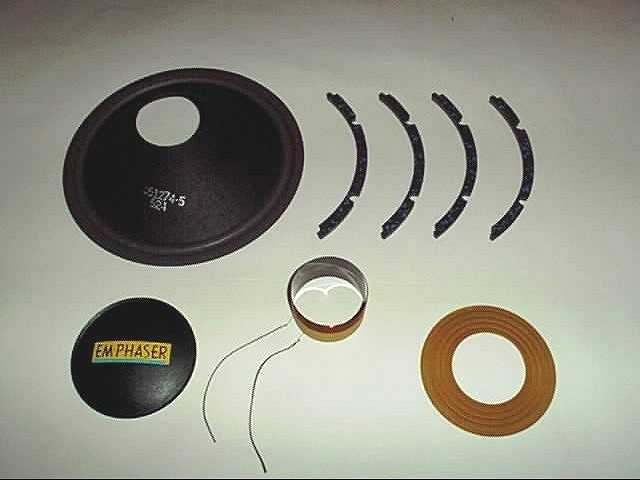
Am Besten fangen wir mit den Bezeichnungen der Einzelteile an, damit es später keine Missverständnisse gibt:
links oben die Membran (der elastische Rand heißt 'Sicke'), rechts daneben der vierteilige 'Gasket' (Dichtring)
unten links die 'Dustcap' (Staubschutzkalotte, ein unmögliches Wort)
unten in der Mitte die Schwingspule (oder auf Neu-Hochdeutsch Voicecoil)
und rechts daneben der Spider (die Zentrierspinne)
Es gibt Recone-Kits (so heißen die Ersatzteilsätze meistens), bei denen die Schwingspule schon exakt in den
Spider eingeklebt ist (z.B. bei EV), oder aber Schwingspule, Spider und Membran schon zusammengeklebt
sind (JBL, FOSTEX). Auch gibt es einteilige Gaskets, wie z.B. bei EV. Aber dazu kommen wir später.
Als Erstes wird die Schwingspule exakt in den Spider eingeklebt. Dazu misst man die Position der alten
Schwingspule aus, um zu wissen, wo der Spider sitzen muss. Dann schiebt man den neuen Spider erst mal
ohne Kleber auf die Schwingspule und positioniert das Ganze exakt so wie das alte Teil. Bleistiftstrich drum-
herum, den Spider etwas beiseite schieben, ca. 1-2 cm³ Zweikomponentenkleber mischen und in eine Spritze.
(von hinten rein, 'aufziehen' geht leider nicht, da der Kleber zu zäh ist). Dann einen dünnen Ring Kleber auf
den Schwingspulenträger neben den Bleistiftstrich 'legen', die Schwingspule wieder in Position 'rutschen'.
Das muss jetzt erst aushärten (dauert je nach Kleber und Temperatur bis zu 24 Std. . . . in den Backofen?)
Das Ganze sieht dann etwa so aus: (Spritze saubermachen nicht vergessen!)
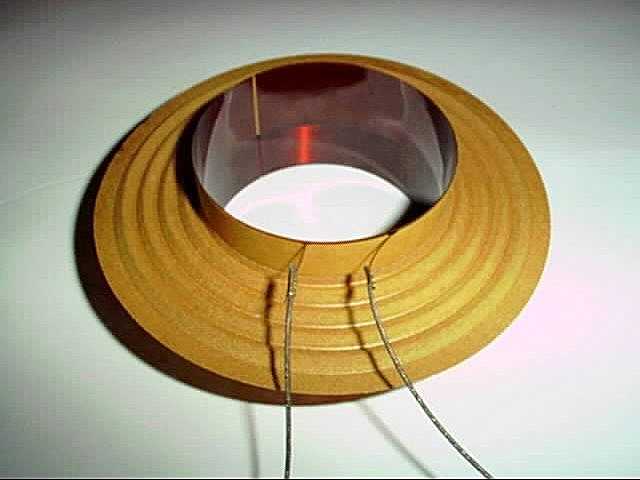
Jetzt haben wir jede Menge Zeit, also schneiden wir die alte Membran samt Schwingspule aus dem Korb heraus.
Sofort danach wird der Luftspalt im Magnetsystem mit Tesapack oder Gaffa abgeklebt, damit keine
Fremdkörper (alter Kleber, abgebrochene Teppichmesserklingen, Membranteile etc.) hineingelangen können.
Die alte Membran sowie Schwingspule unbedingt aufheben! (zum Nachgucken . . .)
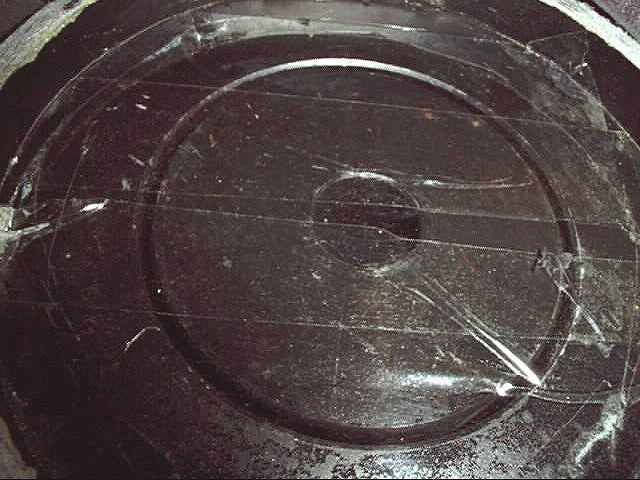
Jetzt kommt der anstrengensde und langweiligste Teil der ganzen Prozedur: der Lautsprecherkorb muss vom
alten Kleber befreit werden. Wenn der Speaker noch nicht zu alt ist, ist es hilfreich, wenn man Korb in den
Heißluftherd legt und auf max. 80°C aufheizt. (Handschuhe!) Dann wird der alte Kleber zäh und man kann
ihn leichter abziehen. Bitte diese Temperatur nicht überschreiten, Neodym-Magnetmaterial z.B. hat eine sehr
niedrige Curie-Temperatur, eine dauerhafte 'Beschädigung' des Magneten wäre die fatale Folge.
Am besten also mit dem Stemmeisen (für alle Nicht-Süddeutschen: Stechbeitel) den alten Kleber cm für cm
abschaben. Und zwar oben (wo die Membransicke angeklebt wird) und auch unten, wo der Spider
festgeklebt werden soll.
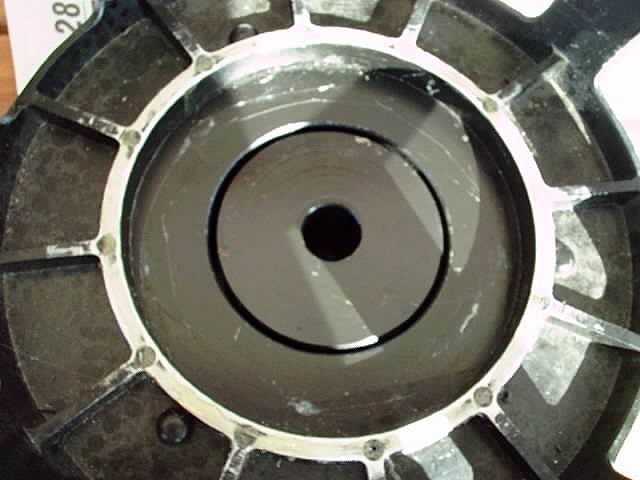
Wenn fertig, kann man das Tesapack wieder entfernen. Der Korb sollte dann so aussehen, wie auf dem Bild. Wenn die Schwingspulenverklebung ausgehärtet ist, geht's weiter: Spider/Schwingspule werden in den Korb
eingeklebt. Dazu müssen die Pappstreifen bereitliegen!
Industriekleber in die Spritze aufziehen und los geht's . . .
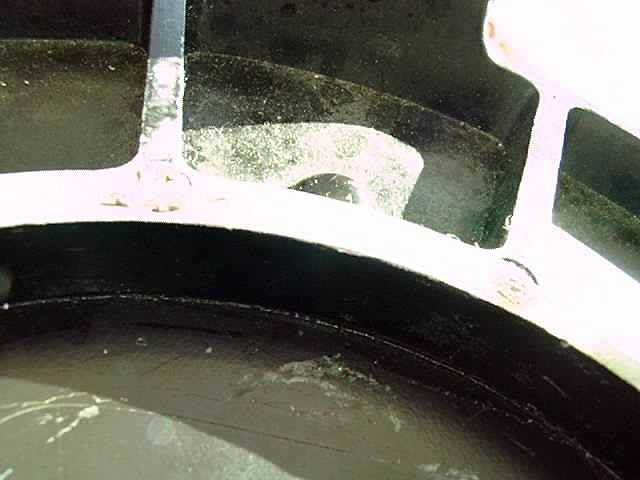
Auf die blanke Alukante kommt ein Ring Kleber aus der Spritze, dann werden Spider/Schwingspule eingesetzt
(die Anschlusskabel zeigen zu den Klemmen!) und sofort mit Hilfe der Pappstreifen zentriert (indem man diese
innerhalb des Schwingspulenträgers in den Luftspalt schiebt).
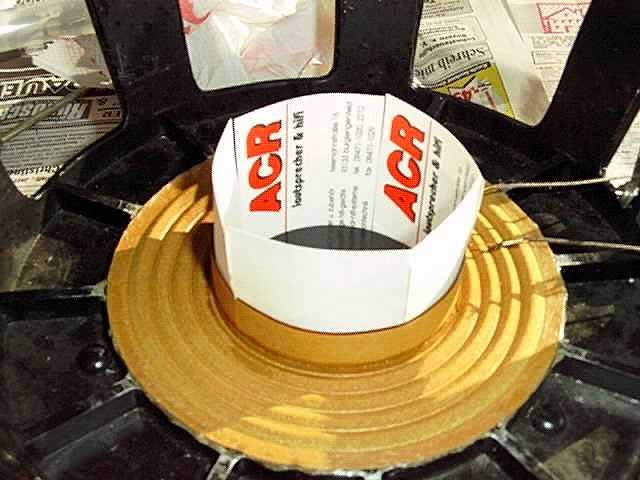
Ich mache dann noch zusätzlich einen Ring Kleber von oben auf den Spider, der Kleber durchdringt das
Gewebe und es ergibt sich eine schöne 'Klebenaht'. Es schadet nicht, wenn man mit dem Finger (bäh!) die
frische Klebestelle mehrmals andrückt! Das muss gut aushärten, am besten über Nacht.
(Spritze saubermachen!)
Als Nächstes wird wiederum Zweikomponentenkleber gemischt und in die Spritze verfrachtet, diesmal aber
mehr. Man legt zuerst einen dünnen (!) Strang auf die Verbindungsstelle Schwingspule/Spider:
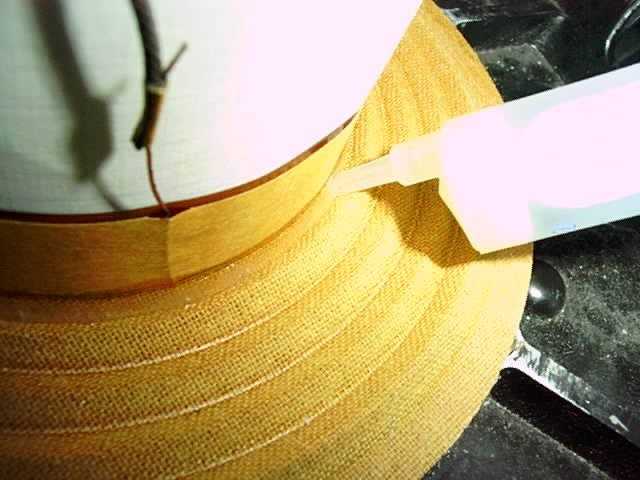
Danach wird sofort die Membran eingesetzt und grade gerückt. In die Verbindungsstelle Membran/Schwingspule
kommt ebenfalls ein Strang Kleber. Der darf ruhig etwas dicker sein . . .
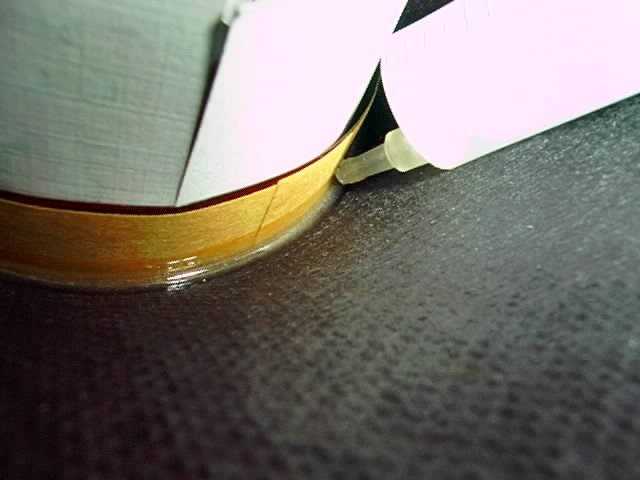
Dort, wo die Anschlusslitzen mal durch die Membran geführt werden, müssen Löcher gestochen werden. (Die
exakte Position von der alten Membran ermitteln! Aha! darum das Zeug aufbewahren . . .)
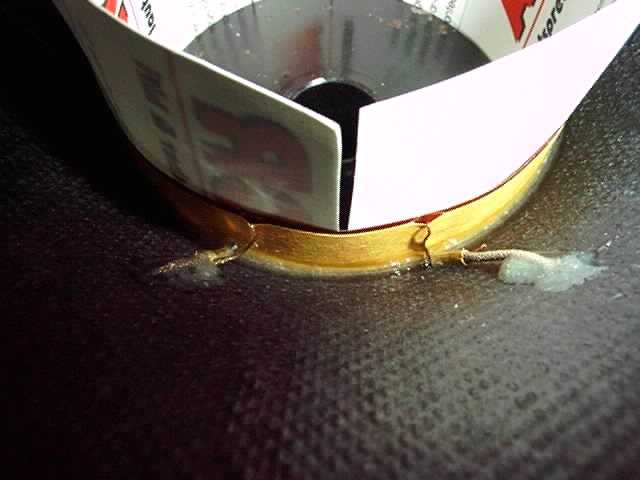
Die Anschlusslitzen durch die Löcher führen und mit Zweikomponentenkleber fixieren.
Wenn alles richtig gemacht wurde, kommen die Litzen auch genau da durch die Membran, wo sich die
Anschlussklemmen befinden! Falls die Membran nicht 'unten bleibt', kreisförmig beschweren (Teller o.ä.).
Aushärten lassen! Backofen? Die Pappstreifen bleiben drin!
Am nächsten Tag wird Industriekleber in die Spritze aufgezogen, es dürfen schon 5-10 cm³ sein!
Damit wird am Korb, dort wo die Sicke (der weiche Rand) der Membran angeklebt werden soll, ein Strang
rund herum gelegt. Dabei muss die Sicke mit der freien Hand hochgebogen werden.
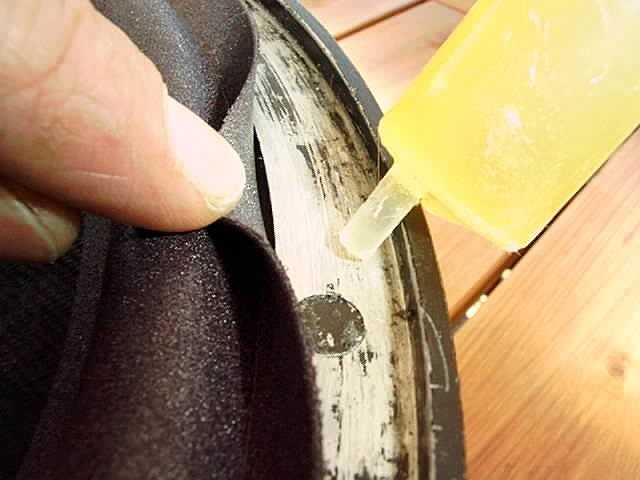
Dann wird die Sicke in den Kleber gedrückt und unmittelbar danach werden die Teile des Gaskets mit
Kleber 'beschichtet' und aufgeklebt.
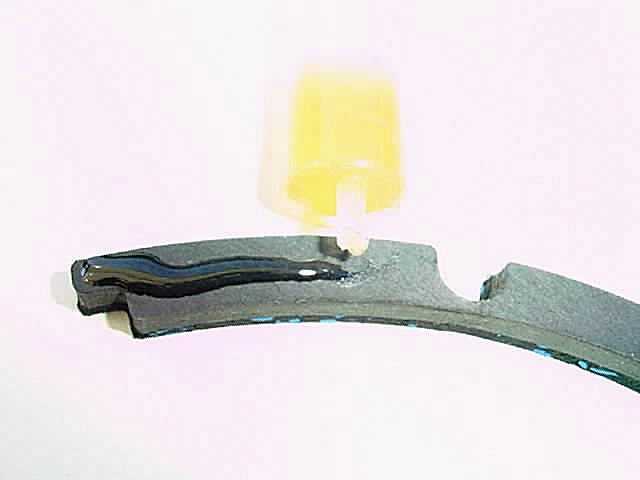
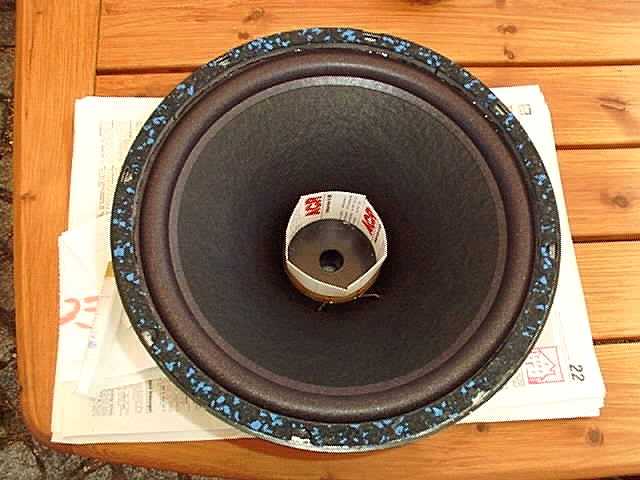
Nachdem deren Position korrigiert wurde (die Befestigungslöcher müssen frei bleiben!),
sieht das Chassis so aus.
Jetzt ist Anpressdruck gefragt! Ich mache das zuerst immer so:
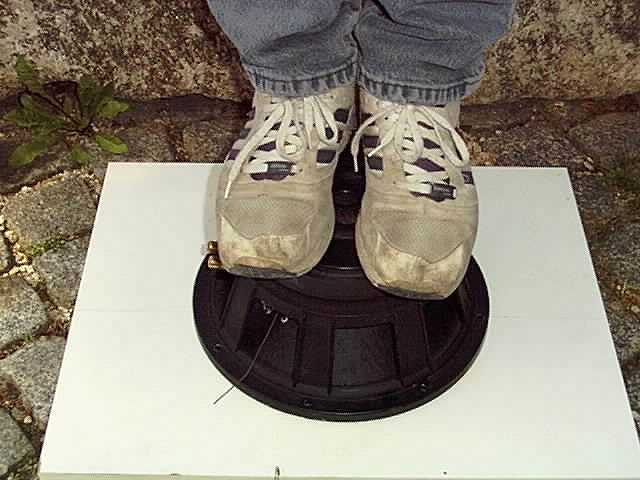
Und nach ein paar Minuten dann so: (die Pappstreifen sind immer noch 'drin'! Spritze sauber machen!)
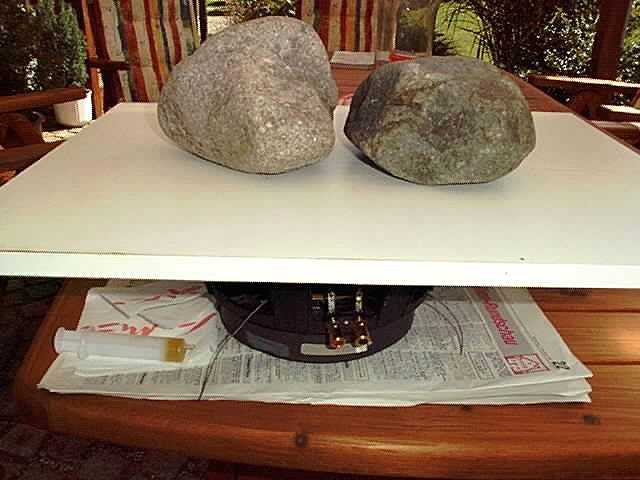
Wenn das ausgehärtet ist, werden die Anschlusslitzen angelötet und gekürzt. Aber nicht stramm spannen,
die Membran muss Bewegungsfreiheit haben!
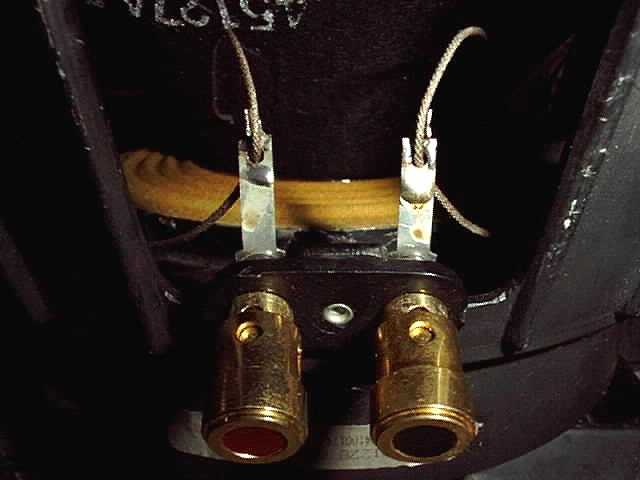
Jetzt werden die Pappstreifen entfernt und man kann schon mal testen, ob die Schwingspule kratzt.
Falls ja, hat man irgendwo was falsch gemacht!!!
Falls nein (gottseidank!), kann man schon mal mit einer 1.5V Batterie testen, was der Speaker 'sagt'.
Als Nächstes wird die Kalotte (ohne Kleber!) auf der Membran zentriert und diese Position wird mit einem
hellen Buntstift (gelb oder weiß) leicht angezeichnet.
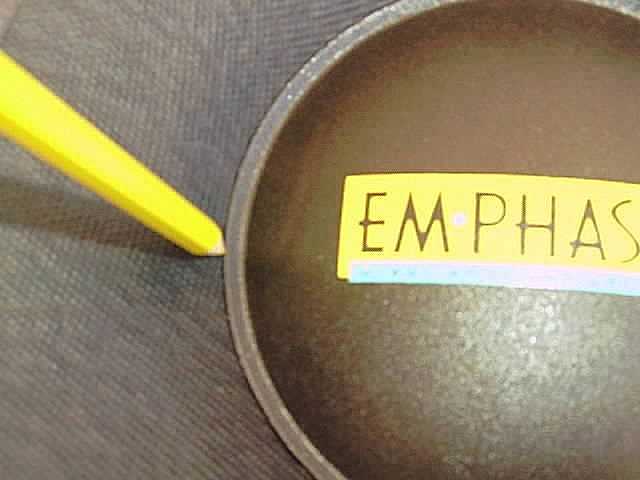
Und jetzt müssen wir ein bisschen 'tricksen', wie sonst sollte man die Staubschutzkalotte von oben anfassen?
Also: mit Hilfe von einem Stück Gaffa oder Isoband einen 'Griff' basteln und auf die Kalotte setzen, aber nicht
zu fest ankleben, das muss ja wieder weg!
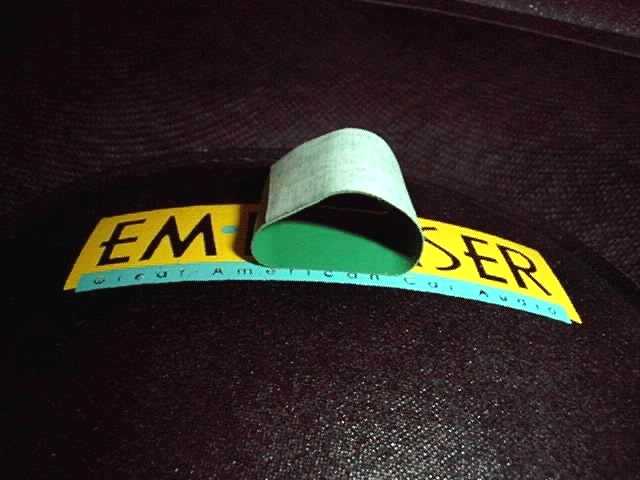
Industriekleber in die Spritze aufziehen und innerhalb des Strichs einen Strang Kleber auf die Membran geben
und auch auf den Kalottenrand, falls dieser hochgebogen ist. Den Kleber etwas antrocknen lassen und dann
die Kalotte passgenau einsetzen. Korrigieren geht leider nicht. Danach den 'Griff' vorsichtig abnehmen und
die Kalotte mit einer (vollen) Getränke- oder Spraydose beschweren. Spritze saubermachen, aushärten lassen!
Ästhetische Menschen achten zusätzlich auch noch auf die Lage des Schriftzuges: Wenn sich
die Anschlussklemmen des Lautsprechers unten befinden, muss der Schriftzug lesbar und waagrecht sein.
Falls die Kalotte keinen umgebogenen Rand besitzt (wie z.B. EV), wird der Kleber nur auf die Membran
aufgetragen, dann die Kalotte eingesetzt, beschwert und danach eine 'Klebenaht' in den v-förmigen Spalt
gelegt. Für diese Verklebung gibt es von EV extra einen Kleber, den Black-Cup-Cement. Der ist allerdings
sauteuer und bildet nach einigen Monaten Klümpchen, so dass der Rest meistens unbrauchbar ist.
Also nehme ich auch hier den Industriekleber.
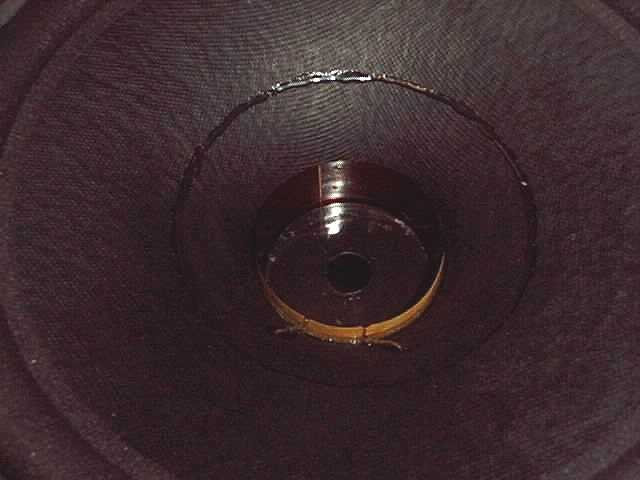
Noch ein Tipp zum Thema Kleber: wer nur ein oder zwei Chassis reparieren will, braucht natürlich kein Kilo
Industriekleber kaufen. Man lässt sich am Besten ein kleines Glas bei jemanden auffüllen, der so eine
Art Kleber verarbeitet (z.B. Schuhmacher: deren 'Schuhsohlenkleber' hat nahezu ideale Eigenschaften)
Nach einem weiteren Tag Wartezeit ist das Chassis wieder einsatzbereit!
2003-05-28 LK |